CORROSION CONSIDERATIONS FOR PRESTIGE PILES
GoliathTech piles/components are in general are designed (both bare and galvanized) using the provisions of AC358 applicable to the following soil parameters/conditions:
Soil Resistivity < 1,000 Ohm-cm
pH level< 5.5
Sulfate Content < 1,000 ppm
For other consideration/soil parameters please read the following details/precisions:
1. GENERAL CONSIDERATIONS
Hot-dip galvanized steel is often utilized in some of the harshest environments imaginable, yet it provides maintenance-free longevity for decades. The corrosion resistance of hot-dip galvanizing varies according to its surrounding environments, but generally corrodes at a rate of 1/30 of bare steel in the same environment. Measurements of the actual consumption rate of the coating during the first few years of service provide good data for projecting a conservative estimate for the remaining life to first maintenance, because as zinc corrosion products build on the surface, which in most environments are adherent and fairly insoluble, the corrosion rate often slows as time progresses. Whether exposed in the atmosphere, subjected to blazing UV rays, snow, and/or other elements, submerged in water, or embedded in soil or concrete, hot-dip galvanized steel an withstand the different corrosive elements and fulfill the intended design life.
2. PILES/COMPONENTS IN ATMOSPHERE
The performance of atmospherically exposed hot-dip galvanized steel depends on five main factors: temperature, humidity, rainfall, sulfur dioxide (pollution) concentration in the air, and air salinity. None of these factors can be singled out as the main contributor to zinc corrosion, but they all play a role in determining the corrosion protection hot-dip galvanized (zinc) coatings can provide in certain atmospheric conditions. Time to first maintenance is defined as 5% rusting of the base steel surface, which means 95% of the zinc coating is still intact, and an initial maintenance is recommended to extend the life of the structure. According to ASTM A123, the governing specification for hot-dip galvanizing, steel ¼-inch thick or greater must have at least 3.9 mils of zinc on the surface, but often, there will be greater than the minimum requirement. Therefore, using the TFM chart, hot-dip galvanized structural steel (>1/4-inch thick) provides 72-73 years of life to first maintenance even in the most corrosive atmosphere, industrial.
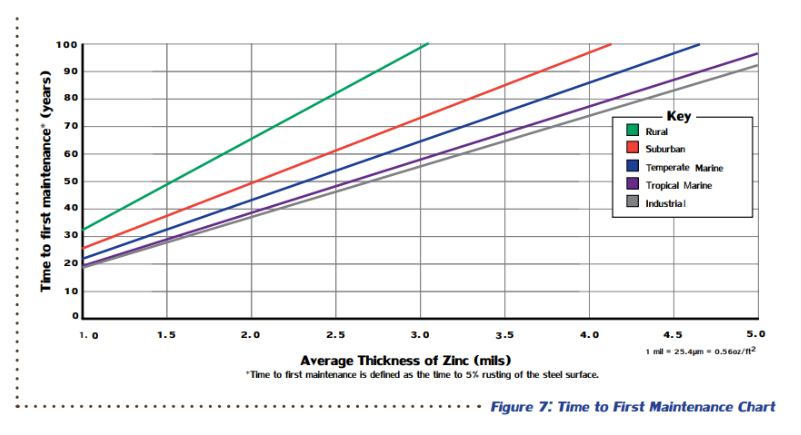
3. PILES/COMPONENTS IN SOIL
Another common exposure for hot-dip galvanized steel is partially or fully buried in soil. With more than 200 different types of soil identified in North America, hot dip galvanizing’s performance in soil is varied and hard to predict. The main factors that dictate the corrosivity of the soil are moisture content, pH level, and chlorides. These soil conditions are affected by additional characteristics such as aeration, temperature, resistivity, and texture or particle size. A general rule of thumb is galvanizing performs well in brown sandy soils, and not as well in gray, clay-like soils. This is because soil with larger particles wick moisture away from the surface more quickly, so the galvanized piece has less exposure to moisture. The first step to estimating the performance of hot-dip galvanized steel in soil is to classify it. And as the corrosion rate of steel in soil can range from less than 20 microns per year in favorable conditions, to 200 microns per year or more in very aggressive soils, misclassifying the soil can lead to unpredicted performance. The AGA has developed a chart for estimating HDG’s performance in soil based on real world corrosion data. In this case, service life is defined as total consumption of the coating plus 25% and is an indication of when the structure should be replaced.
There are four different charts based on the classification of the soil (Figure 8). Using the chart, the first classification is by chloride content — Charts 1 and 2 (top row) are used for soils with high chlorides (>20 PPM) and Charts 3 and 4 (bottom row) are used for soils with low chlorides (<20 PPM) Once you have identified the chloride content, there is a second classification to determine the correct chart to use. For soils with high chlorides, the second determination would be moisture content. Soils with low moisture (17.5%) fall on Chart 2. For low chlorides, the second determination is the pH level. Soils with high pH levels (>7.0) fall on Chart 3, while soils with low pH (< 7.0) falls on chart 4
The blue line on all four charts represents the average for soils surveyed in that characteristic group. The green line represents the best soil in the category sampled, and the red line represents the worst soil in the category from the study. The shaded areas show how the changes in pH and moisture content affect the estimated service life. Assuming 3.5 mils as a minimum thickness for HDG buried in soil, the chart shows the average life in the harshest soils (uncommon) would be approximately 50 years and in the best soils exceed 120 years

4. PILES/COMPONENTS IN WATER
A less common environment for galvanized steel is submerged in or exposed to water. Moisture is highly corrosive to most metals including steel and zinc. However, because of the development of the passive, mostly non-soluble zinc patina, the corrosion rate of galvanized steel is much slower than bare steel. There are many different types of water (pure water, natural fresh water, potable water (treated drinking water), and seawater) and each has different mechanisms that determine the corrosion rate. Similar to soils, the varieties of water make predicting corrosion rates difficult. Though pH level has the most profound effect, many parameters affect corrosion of metals in a water environment including oxygen content, water temperature, agitation, the presence of inhibitors, and tide conditions. Despite the difficulty of predicting corrosion, hot-dip galvanizing steel is one of the best methods of corrosion protection for submersed applications because of its complete, uniform coverage. Water with high free oxygen or carbon dioxide content is more corrosive than water containing less of these gases, and hard water is much less corrosive than soft water. A natural scale of insoluble salts tends to form on the galvanized surface under conditions of moderate or high-water hardness. The salts combine with zinc to form a protective barrier of calcium carbonate and basic zinc carbonate. Similar to fresh water, galvanized coatings provide considerable protection to steel when immersed in sea water and exposed to salt spray. Influencing factors in the corrosion of zinc in fresh water also apply to sea water; however, the dissolved salts (primarily sulfides and chlorides) in sea water are the principal determinants of the corrosion behavior of zinc. Given the high level of chloride in sea water, a very high corrosion rate might be expected. However, the presence of magnesium and calcium ions has a strong inhibiting effect on zinc corrosion.
5. PILES/COMPONENTS IN CONCRETE
Concrete is an extremely complex material. The use of various types of concrete in construction has made the chemical, physical, and mechanical properties of concrete and its relationship to metals a topic of ongoing studies. Reinforcing steel bars (rebar) are embedded in concrete to provide strength and are critical to the integrity and performance of the structure throughout its life. As concrete is a porous material, corrosive elements such as water, chloride ions, oxygen, carbon dioxide, and other gasses travel into the concrete matrix, eventually reaching the rebar. Once the concentration of these corrosive elements surpasses steel’s corrosion threshold, the rebar starts to corrode. As the rebar corrodes, pressure builds around the bar leading to cracking, staining, and eventually spalling of the concrete (Figure 9). Because failure of the rebar leads to compromised or failing structural capacity, protecting against premature rebar failure is key. Similar to in the atmosphere, galvanized rebar extends the life of the steel in concrete. The corrosion mechanisms in concrete are quite different than atmospheric exposure, and one of the biggest factors is chloride concentration. Galvanized rebar can withstand chloride concentration at least four to five times higher than black steel, and remains passivated at lower pH levels, slowing the rate of corrosion. In addition to the higher chloride tolerance, once zinc corrosion products are formed from the galvanized rebar, they are less voluminous than iron oxide and actually migrate away from the bar. Figure 10 shows the white zinc particles migration away from the bar (galvanized coating) and into the pores of the concrete matrix. This migration prevents the pressure buildup and spalling caused by iron oxide particles. The total life of galvanized steel in concrete is made up of the time taken for the zinc to de-passivate, plus the time taken for consumption of the zinc coating, as it sacrificially protects the underlying steel. Only after the coating has been fully consumed in a region of the bar will localize steel corrosion begin.


CORROSION CONSIDERATIONS FOR VENTURA PILES
GoliathTech VENTURA piles/components are in general are designed using the provisions of
AC358 applicable to the following soil parameters/conditions:
Soil Resistivity < 1,000 Ohm-cm
pH level< 5.5
Sulfate Content < 1,000 ppm
50 Year life
For other consideration/soil parameters and different life please consider the following:
1. GENERAL PROCEDURE
Structural pile capacity must be assessed/calculated using the appropriate sacrificial thickness based on the tables presented below Amount of the sacrificial thickness will depend on the following parameters:
a- Soil Conditions
b- The lifetime life of the structure
Please check for the applicable local regulations and standards in terms of the amount of sacrificial thickness applicable for your project corrosive environment.
2. PILES/COMPONENTS IN ATMOSPHERE
The performance of atmospherically exposed hot-dip galvanized steel depends on five main factors: temperature, humidity, rainfall, sulfur dioxide (pollution) concentration in the air, and air salinity. None of these factors can be singled out as the main contributor to zinc corrosion, but they all play a role in determining the corrosion protection hot-dip galvanized (zinc) coatings can provide in certain atmospheric conditions.
Time to first maintenance is defined as 5% rusting of the base steel surface, which means 95% of the zinc coating is still intact, and an initial maintenance is recommended to extend the life of the structure. According to ASTM A123, the governing specification for hot-dip galvanizing, steel ¼-inch thick or greater must have at least 3.9 mils of zinc on the surface, but often, there will be greater than the minimum requirement. Therefore, using the TFM chart, hot-dip galvanized structural steel (>1/4-inch thick) provides 72-73 years of life to first maintenance even in the most corrosive atmosphere, industrial.

3. PILES/COMPONENTS IN SOIL WITH OR WITHOUT WATER TABLE
Please estimate the necessary sacrificial thickness (mm) on the following table (Table 4.2 EC 7) with an emphasis on life requirement greater than 50 years. More detail assessment of the soil conditions may be warranted or/and recommended.
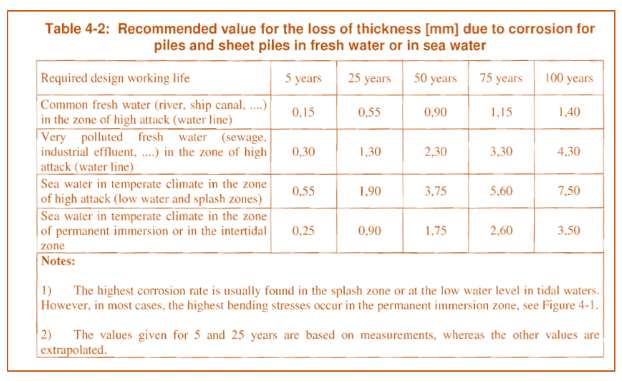
4. PILES/COMPONENTS IN WATER
Please estimate the necessary sacrificial thickness (mm) on the following table (Table 4.2 EC 7) with an emphasis on life requirement greater than 50 years. More detail assessment of the water corrosivity may be warranted or/and recommended.
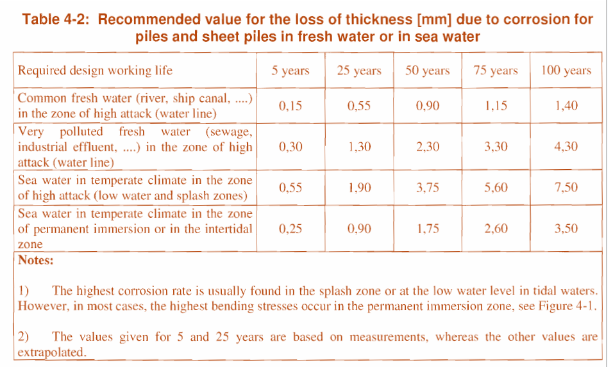
5. PILES/COMPONENTS IN CONCRETE
The corrosion mechanisms and performance of black is different than when exposed to atmospheric conditions. Steel embedded in concrete is exposed to a highly alkaline environment. Black steel is passive in alkaline concrete until the chloride level exceeds approximately 1 lb/yd 3 , when steel becomes depassivated and starts to corrode.
Chlorides penetrate the concrete through small pores and cracks that form on the surface through use and weathering. Black steel in concrete typically depassivates below a pH of 11.5.
When steel reinforcement is encased in sound dense concrete, the entire surface of the steel is covered by a stable protective oxide film that forms in the alkaline environment created by the hydration of the cement in the concrete. Under these circumstances no corrosion of the reinforcement can occur. However, if the protective oxide film is locally destroyed, for example by the ingress of chloride ions, areas of different potential can be set up on the surface. Reference to the galvanic series shown in Table 1 shows that
steel encased in concrete with its protective film intact will have a more noble potential than steel without the protection of the alkaline environment. This difference in potential can result in electrochemical corrosion cells forming between areas on the reinforcement where the protective film has been destroyed and the remainder of the surface where the film is still intact. Such cells create minute electric currents which flow through the reinforcement in one direction and return through the concrete by electrolytic conduction.
The areas where the electrons leave the reinforcement to enter the concrete are called anodes and they corrode, whereas the areas where the current re-enters the reinforcement do not corrode and are called cathodes. Corrosion takes place at the anode with metal ions going into solution (refer Eqn. 1) Fe-->Fe++ + 2e- (1). No corrosion occurs at the cathode, the cathode simply provides the mechanism for the removal of electrons left in the reinforcement by the corrosion process (refer Eqn. 2). O2+2H2O + 4e--> 4OH- (2).
The concrete must be wet enough to provide an electrolytic path for the transport of ions and therefore the corrosion of reinforcement in dry concrete is minimal even if areas of different potential exist. There are two ways that the protective oxide film that forms on steel reinforcement in sound concrete might be destroyed. These are the reduction of the pH of the concrete by carbonation, and the ingress of chloride ions.
MECHANISMS OF CORROSION OF STEEL IN CONCRETE
From the above discussions, it is apparent that three conditions have to be present to allow significant corrosion of steel reinforcement in a concrete structure, namely:
- (i) disruption of the protective iron oxide film to form an anodic site
- (ii) a supply of oxygen to remove electrons remaining from the anodic reaction, and
- (iii) the concrete being conductive enough to allow corrosion currents to flow. Disruption of the protective oxide film can be caused by the ingress of chloride ions and/or loss of alkalinity due to carbonation. Areas without the protective oxide film will corrode and the rate of corrosion in most cases will be governed either by the diffusion of oxygen to the cathode areas or the resistivity (dryness) of the concrete.
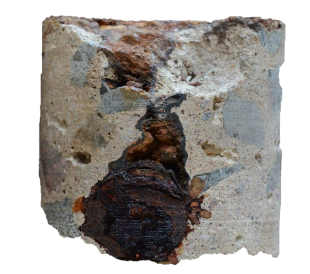
Source : American Galvanizers Association
No matter what your project is…
GoliathTech helical piles are ready
In order to provide you with a helical (screw) pile foundation solution that’s designed to meet your needs and specific project, our network of certified installers and consultants make the most of their vast expertise in the field. Recognized for their know-how, they conform screw piles to meet the unique nature of your property and project, rather than offering you a solution… cast in concrete!