CONSIDÉRATIONS SUR LA CORROSION POUR LES PIEUX PRESTIGE
Les pieux/composants GoliathTech sont en général conçus (à la fois nus et galvanisés) en utilisant les dispositions de l'AC358 applicables aux paramètres/conditions de sol suivants :
Résistivité du sol < 1 000 Ohm-cm
Niveau de pH < 5,5
Teneur en sulfate < 1 000 ppm
Pour d’autres considérations/paramètres du sol, veuillez lire les détails/précisions suivants :
1. CONSIDÉRATIONS GÉNÉRALES
Les performances de l'acier galvanisé à chaud exposé aux conditions atmosphériques dépendent de cinq facteurs principaux : la température, l'humidité, les précipitations, la concentration de dioxyde de soufre (pollution) dans l'air et la salinité de l'air. Aucun de ces facteurs ne peut être identifié comme le principal contributeur à la corrosion du zinc, mais ils jouent tous un rôle dans la détermination de la protection contre la corrosion que les revêtements galvanisés à chaud (zinc) peuvent fournir dans certaines conditions atmosphériques. Le délai avant le premier entretien est défini comme 5 % de rouille de la surface de l'acier de base, ce qui signifie 95 % de la le revêtement de zinc est encore intact, et un premier entretien est recommandé pour prolonger la durée de vie de la structure. Selon ASTM A123, la spécification régissant pour galvanisation à chaud, acier de ¼ de pouce d'épaisseur ou plus doit avoir au moins 3,9 mils de zinc en surface, mais le plus souvent, il y aura plus que l’exigence minimale. Par conséquent, en utilisant le TFM graphique, acier de construction galvanisé à chaud (> 1/4 de pouce épais) offre une durée de vie de 72 à 73 ans jusqu'au premier entretien même dans les atmosphères les plus corrosives, industrielles.
2. PIEUX/COMPOSANTS EN ATMOSPHÈRE
Les performances de l'acier galvanisé à chaud exposé aux conditions atmosphériques dépendent de cinq facteurs principaux : la température, l'humidité, les précipitations, la concentration de dioxyde de soufre (pollution) dans l'air et la salinité de l'air. Aucun de ces facteurs ne peut être identifié comme le principal contributeur à la corrosion du zinc, mais ils jouent tous un rôle dans la détermination de la protection contre la corrosion que les revêtements galvanisés à chaud (zinc) peuvent fournir dans certaines conditions atmosphériques.
Le délai avant le premier entretien est défini comme 5 % de rouille de la surface de l'acier de base, ce qui signifie 95 % du revêtement de zinc est encore intact, et un premier entretien est recommandé pour prolonger la durée de vie de la structure. Selon ASTM A123, la spécification régissant pour galvanisation à chaud, acier de ¼ de pouce d'épaisseur ou plus doit avoir au moins 3,9 mils de zinc en surface, mais le plus souvent, il y aura plus que l’exigence minimale. Par conséquent, en utilisant le TFM graphique, acier de construction galvanisé à chaud (> 1/4 de pouce épais) offre une durée de vie de 72 à 73 ans jusqu'au premier entretien même dans les atmosphères les plus corrosives, industrielles.
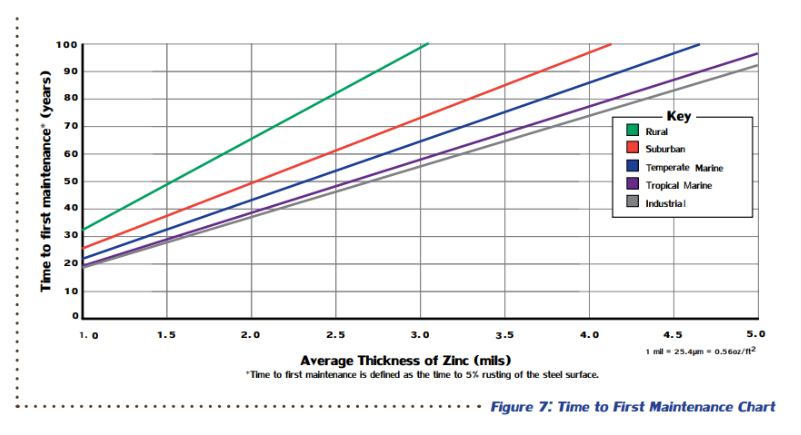
3. PIEUX/COMPOSANTS DANS LE SOL
Une autre exposition courante pour l'acier galvanisé à chaud est partiellement ou entièrement enfoui dans le sol. Avec plus de 200 différents types de sols identifiés en Amérique du Nord, les
performances de la galvanisation à chaud dans le sol sont variées et difficiles à évaluer et prédire. Les principaux facteurs qui dictent la corrosivité du le sol sont la teneur en humidité, le niveau de pH et les chlorures. Ces les conditions du sol sont affectées par des caractéristiques supplémentaires tels que l'aération, la température, la résistivité et la texture ou la taille des particules. Une règle générale est de galvaniser donne de bons résultats dans les sols sablonneux bruns, mais moins bien dans les sols gris et argileux. En effet, les sols contenant des particules plus grosses évacuent l'humidité de la surface plus rapidement afin que la pièce galvanisée est moins exposée à l’humidité. La première étape pour estimer les performances du bain à chaud l'acier galvanisé dans le sol est de le classer. Et comme la corrosion le taux d'acier dans le sol peut varier de moins de 20 microns par an dans des conditions favorables, jusqu'à 200 microns par an ou plus dans des sols très agressifs, une mauvaise classification du sol peut conduire à des performances imprévues. L'AGA a développé un graphique pour estimer les performances du HDG dans les sols sur des données réelles de corrosion. Dans ce cas, la durée de vie est définie comme la consommation totale du revêtement majorée de 25 %, et est une indication du moment où la structure doit être remplacée.
Il existe quatre cartes différentes basées sur la classification du sol (Figure 8). À l'aide du graphique, la première classification se fait par teneur en chlorures — Les graphiques 1 et 2
(rangée du haut) sont utilisés pour les sols à forte teneur en chlorures (>20 PPM) et les graphiques 3 et 4 (rangée du bas) sont utilisés pour les sols à faible teneur en chlorures (< 20
PPM) Une fois que vous avez identifié la teneur en chlorure, il existe une deuxième classification pour déterminer le tableau correct à utiliser. Pour les sols riches en chlorures, la deuxième détermination serait la teneur en humidité. Les sols à faible humidité (17,5 %) figurent dans le graphique 2. Pour les sols à faible teneur en chlorures, la deuxième détermination est le niveau de pH. Les sols avec un pH élevé (>7,0) figurent dans le graphique 3, tandis que les sols avec un pH faible (<7,0) figurent dans le graphique 4.
La ligne bleue sur les quatre graphiques représente la moyenne des sols étudiés dans ce groupe caractéristique. La ligne verte représente le meilleur sol de la catégorie échantillonnée et la ligne rouge représente le pire sol de la catégorie de l'étude. Les zones ombrées montrent comment les changements de pH et de teneur en humidité affectent la durée de vie estimée. En supposant une épaisseur minimale de 3,5 mils pour le HDG enfoui dans le sol, le graphique montre que la durée de vie moyenne dans les sols les plus durs (rare) serait d'environ 50 ans et que dans les meilleurs sols, elle dépasserait 120 ans.

4. PIEUX/COMPOSANTS DANS L'EAU
Un environnement moins courant pour l’acier galvanisé est immergé ou exposé à l’eau. L'humidité est très corrosive pour la plupart des métaux, notamment l'acier et le zinc. Cependant, en raison du développement d’une patine de zinc passive, généralement insoluble, le taux de corrosion de l’acier galvanisé est beaucoup plus lent que celui de l’acier nu. Il existe de nombreux types d’eau différents (eau pure, eau douce naturelle, eau potable (eau potable traitée) et eau de mer) et chacun possède des mécanismes différents qui déterminent le taux de corrosion. À l’instar des sols, les variétés d’eau rendent difficile la prévision des taux de corrosion. Bien que le niveau de pH ait l'effet le plus profond, de nombreux paramètres affectent la corrosion des métaux dans un environnement aquatique, notamment la teneur en oxygène, la température de l'eau, l'agitation, la présence d'inhibiteurs et les conditions de marée. Malgré la difficulté de prédire la corrosion, l'acier galvanisé à chaud est l'une des meilleures méthodes de protection contre la corrosion pour les applications immergées en raison de sa couverture complète et uniforme. L'eau à forte teneur en oxygène libre ou en dioxyde de carbone est plus corrosive que l'eau contenant moins de ces gaz, et l'eau dure est beaucoup moins corrosive que l'eau contenant moins de ces gaz , et l’eau dure est beaucoup moins corrosive que l’eau douce. Un tartre naturel de sels insolubles a tendance à se former sur la surface galvanisée dans des conditions de dureté de l'eau modérée ou élevée. Les sels se combinent avec le zinc pour former une barrière protectrice de carbonate de calcium et de carbonate de zinc basique. Semblables à
l’eau douce, les revêtements galvanisés offrent une protection considérable à l’acier lorsqu’il est immergé dans l’eau de mer et exposé aux brouillards salins. Les facteurs influençant la corrosion du zinc dans l’eau douce s’appliquent également à l’eau de mer ; cependant, les sels dissous (principalement les sulfures et les chlorures) dans l'eau de mer sont les principaux déterminants du comportement à la corrosion du zinc. Compte tenu du niveau élevé de chlorure dans l’eau de mer, on peut s’attendre à un taux de corrosion très élevé. Cependant, la présence d’ions magnésium et calcium a un fort effet inhibiteur sur la corrosion du zinc.
5. PIEUX/COMPOSANTS EN BÉTON
Le béton est un matériau extrêmement complexe. L'utilisation de divers types de béton dans la construction a fait des propriétés chimiques, physiques et mécaniques du béton et de ses relations avec les métaux un sujet d'études en cours. Les barres d'armature en acier (barres d'armature) sont noyées dans le béton pour assurer leur résistance et sont essentielles à l'intégrité et aux performances de la structure tout au long de sa durée de vie. Le béton étant un matériau poreux, les éléments corrosifs tels que l’eau, les ions chlorure, l’oxygène, le dioxyde de carbone et d’autres gaz pénètrent dans la matrice du béton et finissent par atteindre les barres d’armature. Une fois que la concentration de ces éléments corrosifs dépasse le seuil de corrosion de l’acier, les barres d’armature commencent à se corroder. À mesure que la barre d'armature se corrode, la pression s'accumule autour de la barre, entraînant des fissures, des taches et éventuellement un effritement du béton (Figure 9).
Étant donné que la défaillance des barres d’armature entraîne une capacité structurelle compromise ou défaillante, il est essentiel de se protéger contre une défaillance prématurée des barres d’armature. Semblable à l'atmosphère, les barres d'armature galvanisées prolongent la durée de vie de l'acier dans le béton. Les mécanismes de corrosion du béton sont très différents de ceux de l’exposition atmosphérique, et l’un des facteurs les plus importants est la concentration en chlorure. Les barres d'armature galvanisées peuvent résister à une concentration de chlorure au moins quatre à cinq fois supérieure à celle de l'acier noir et restent passivées à des niveaux de pH inférieurs, ralentissant ainsi le taux de corrosion. En plus de la tolérance plus élevée au chlorure, une fois que les produits de corrosion du zinc sont formés à partir de la barre d'armature galvanisée, ils sont moins volumineux que l'oxyde de fer et s'éloignent de la barre.
La figure 10 montre la migration des particules de zinc blanc loin de la barre (revêtement galvanisé) et dans les pores de la matrice de béton. Cette migration empêche l’accumulation de pression et l’écaillage provoqués par les particules d’oxyde de fer. La durée de vie totale de l'acier galvanisé dans le béton est composée du temps nécessaire à la de passivation du zinc, plus le temps nécessaire à la consommation du revêtement de zinc, car il protège de manière sacrificielle l'acier sous-jacent. Ce n’est qu’une fois que le revêtement a été entièrement consommé dans une région de la barre que la corrosion localisée de l’acier commence.


CONSIDÉRATIONS SUR LA CORROSION POUR LES PIEUX VENTURA
Les pieux/composants GoliathTech sont en général conçus (à la fois nus et galvanisés) en utilisant les dispositions de l'AC358 applicables aux paramètres/conditions de sol suivants :
Résistivité du sol < 1 000 Ohm-cm
Niveau de pH < 5,5
Teneur en sulfate < 1 000 ppm
Durée de vie de 50 ans
Pour d'autres considérations/paramètres du sol et une durée de vie différente, veuillez considérer ce qui suit:
1. PROCÉDURE GÉNÉRALE
La capacité structurelle des pieux doit être évaluée/calculée en utilisant l'épaisseur sacrificielle appropriée en fonction des tableaux présentés ci-dessous.
L'ampleur de l'épaisseur sacrificielle dépendra des paramètres suivants :
- a- Conditions du sol
- b- La durée de vie de la structure
Veuillez vérifier les réglementations et normes locales applicables en termes de quantité d'épaisseur sacrificielle applicable à l'environnement corrosif de votre projet.
2. PIEUX/COMPOSANTS EN ATMOSPHÈRE
Les performances de l'acier galvanisé à chaud exposé aux conditions atmosphériques dépendent de cinq facteurs principaux : la température, l'humidité, les précipitations, la concentration de dioxyde de soufre (pollution) dans l'air et la salinité de l'air. Aucun de ces facteurs ne peut être identifié comme le principal contributeur à la corrosion du zinc, mais ils jouent tous un rôle dans la détermination de la protection contre la corrosion que les revêtements galvanisés à chaud (zinc) peuvent fournir dans certaines conditions atmosphériques.
Le délai avant le premier entretien est défini comme 5 % de rouille de la surface de l'acier de base, ce qui signifie 95 % de la le revêtement de zinc est encore intact, et un premier entretien est recommandé pour prolonger la durée de vie de la structure. Selon ASTM A123, la spécification régissant pour galvanisation à chaud, acier de ¼ de pouce d'épaisseur ou plus doit avoir au moins 3,9 mils de zinc en surface, mais le plus souvent, il y aura plus que l’exigence minimale. Par conséquent, en utilisant le TFM graphique, acier de construction galvanisé à chaud (> 1/4 de pouce épais) offre une durée de vie de 72 à 73 ans jusqu'au premier entretien même dans les atmosphères les plus corrosives, industrielles.
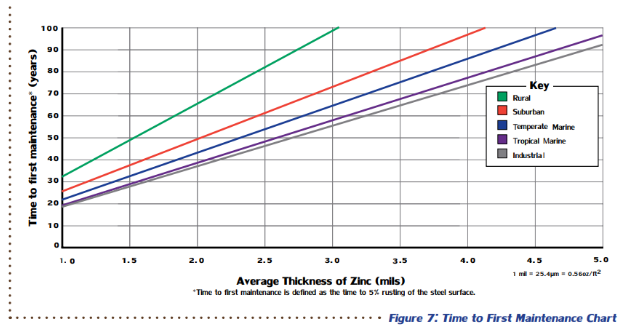
3. PIEUX/COMPOSANTS DANS UN SOL AVEC OU SANS NAPPE PHRÉATIQUE
Veuillez estimer l'épaisseur sacrificielle nécessaire (mm) sur le tableau suivant (Tableau 4.2 EC 7) en mettant l'accent sur l'exigence de durée de vie supérieure à 50 ans.
Une évaluation plus détaillée des conditions du sol peut être justifiée ou/et recommandée.
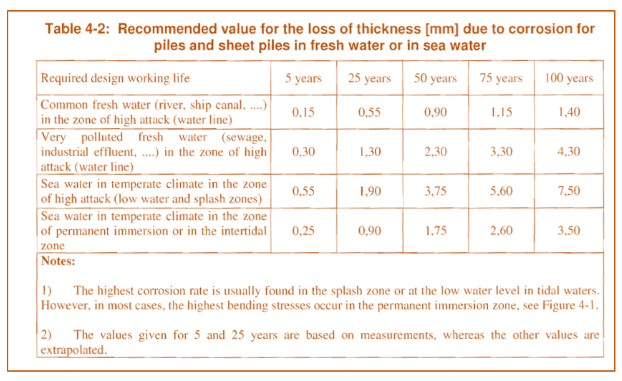
4. PIEUX/COMPOSANTS DANS L’EAU
Veuillez estimer l'épaisseur sacrificielle nécessaire (mm) sur le tableau suivant (Tableau 4.2 EC 7) en mettant l'accent sur l'exigence de durée de vie supérieure à 50 ans.
Une évaluation plus détaillée de la corrosivité de l'eau peut être justifiée ou/et recommandée.
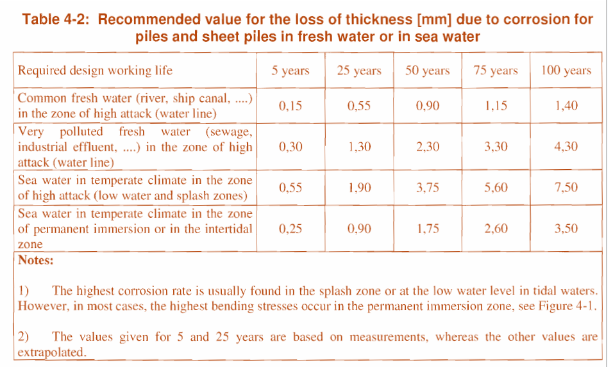
5. PIEUX/COMPOSANTS EN BÉTON
Les mécanismes de corrosion et les performances du noir sont différents de ceux exposés aux conditions atmosphériques. L'acier noyé dans le béton est exposé à un environnement hautement alcalin. L'acier noir est passif dans le béton alcalin jusqu'à ce que le niveau de chlorure dépasse environ 1 lb/yd3, lorsque l'acier devient dépassivé et commence à se corroder.
Les chlorures pénètrent dans le béton à travers les petits pores et les fissures qui se forment à la surface sous l'effet de l'utilisation et des intempéries. L'acier noir dans le béton dépassive généralement en dessous d'un pH de 11,5
Lorsque l'armature en acier est enveloppée dans un béton dense et sain, toute la surface de l'acier est recouverte d'un film d'oxyde protecteur stable qui se forme dans l'environnement alcalin créé par l'hydratation du ciment dans le béton. Dans ces circonstances, aucune corrosion du renfort ne peut se produire. Cependant, si le film d'oxyde protecteur est détruit localement, par exemple par la pénétration d'ions chlorure, des zones de potentiel différent peuvent se former à la surface. La référence aux séries galvaniques présentées dans le tableau 1 montre que l'acier enrobé de béton avec son film protecteur intact aura un potentiel plus noble que l'acier sans la protection de l'environnement alcalin. Cette différence de potentiel peut entraîner la formation de cellules de corrosion électrochimique entre les zones du renfort où le film protecteur a été détruit et le reste de la surface où le film est encore intact.
De telles cellules créent de minuscules courants électriques qui traversent les armatures dans une direction et reviennent à travers le béton par conduction électrolytique.
Les zones où les électrons quittent l'armature pour entrer dans le béton sont appelées anodes et se corrodent, tandis que les zones où le courant rentre dans l'armature ne se corrodent pas et sont appelées cathodes. La corrosion a lieu à l'anode avec des ions métalliques entrant en solution (voir équation 1) Fe --> Fe++ + 2e- (1) Aucune corrosion ne se produit à la cathode, la cathode fournit simplement le mécanisme d'élimination des électrons laissés dans le renfort par le processus de corrosion (voir l’équation 2). O2 + 2H2O + 4e- --> 4OH- (2)
Le béton doit être suffisamment humide pour fournir un chemin électrolytique pour le transport des ions et donc la corrosion des armatures dans le béton sec est minime même s'il existe des zones de potentiel différent. Le film protecteur d'oxyde qui se forme sur les armatures en acier dans le béton sain peut être détruit de deux manières. Il s'agit de la réduction du pH du béton par carbonatation et de la pénétration d'ions chlorure.
MÉCANISMES DE CORROSION DE L'ACIER DANS LE BÉTON
Des discussions ci-dessus, il ressort que trois conditions doivent être réunies pour permettre une corrosion significative des armatures en acier dans une structure en béton, à savoir :
- (i) rupture du film protecteur d'oxyde de fer pour former un site anodique
- (ii) un apport d'oxygène pour éliminer les électrons restant de la réaction anodique, et
- (iii) le béton soit suffisamment conducteur pour permettre aux courants de corrosion de circuler. La rupture du film protecteur d'oxyde peut être provoquée par la pénétration d'ions chlorure et/ou par une perte d'alcalinité due à la carbonatation. Les zones sans film d'oxyde protecteur se corroderont et le taux de corrosion sera dans la plupart des cas régi par la diffusion de l'oxygène vers les zones cathodiques ou par la résistivité (sécheresse) du béton.
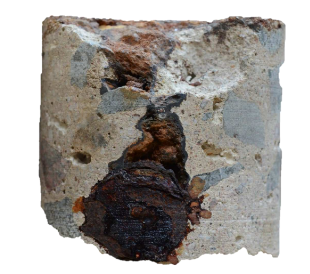
Source : American Galvanizers Association
Peu importe votre projet…
Les pieux vissés GoliathTech sont toujours prêts.
Dans le but de vous offrir une solution de fondation sur pieux vissés qui soit parfaitement adaptée à vos besoins et à votre projet, notre réseau d’installateurs certifiés met à profit sa vaste expertise sur le terrain. Reconnus pour leur savoir-faire, ils adapteront les pieux à hélice selon la nature unique de votre terrain et de votre projet plutôt que de vous offrir une solution… coulée dans le béton!